EMS supports Pincroft Dyeing & Printing through specialised Permit Training
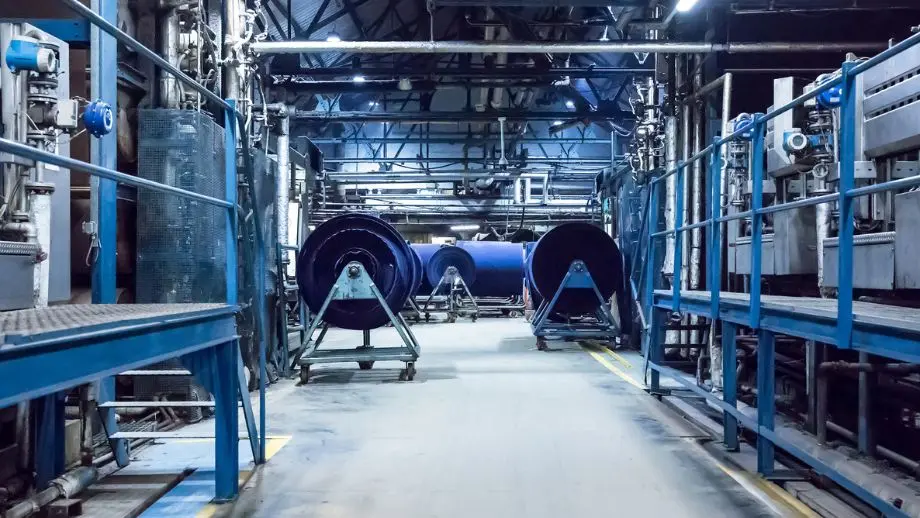
Pincroft has had an environmental permit with Environment Agency (EA) for around 10 years, with their Health, Safety and Environment (SHE) Officer being responsible for the permit. It is of high importance that the rest of the business and the senior leadership team are also made aware of what exactly the permit requirements are.
The training provided by EMS gave an insight into reasons why a permit is needed, consequences of non-compliance and potential environmental impacts. The training involved activities to engage employees with the permit and it examined the individual parts of the permit.
The Client
Pincroft Dyeing and Printing specialises in textile bleaching, dyeing, and large-scale printing, operating from a state-of-the-art facility in Adlington.
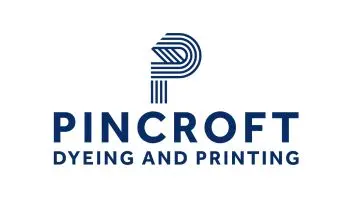
Client Benefits
Our dedicated training team is comprised of practicing environmental consultants. As part of their day-to-day role, our trainers work with some of the UK’s largest organisations to help them maintain compliance with environmental legislation. This means that our team is positioned perfectly to deliver training content as well as real-world advice and working case-studies.
- Higher level of awareness around their environmental impacts
- Encourages involvement of whole senior leadership team
- A better understanding of the scope and requirements of a permit, incorporating parts of a permit such as emissions, Schedule 5, and accidents and near misses
- Encourages a proactive approach to environmental management, so greater oversight of environmental impacts
- Our dedicated training team is comprised of practicing environmental consultants.
The Challenges
Pincroft faced the challenge of ensuring that not only their Health and Safety team, but also senior leadership and other employees were fully equipped to interpret and comply with their environmental permit. Without this, a company may risk non-compliance and potential penalties.
A SHE Officer was responsible for the permit, but the senior leadership team also needed to be aware of what the permit required of them. While in many cases SHE Officers may be responsible for an environmental permit within an organisation, it is often of great importance that senior leadership within a business or organisation are also aware of what exactly their environmental permit requires.
The EA encourage sites to have permit training – it is no longer just a “nice to have”.
The Solution
As part of their day-to-day role, our trainers work with some of the UK’s largest organisations to help them maintain compliance with environmental legislation. This means that our team is well positioned to deliver training content as well as practical advice.
EMS provided permit training to ensure that all necessary Pincroft staff were aware of their obligations under their environmental permit, and of the consequences of non-compliance.
This meant breaking down their responsibilities regarding monitoring emissions to air or water, raising awareness among staff, and giving an insight into why a permit is needed.
For example, part of the permit touched on stack emissions testing requirements. Stack testing reports were cross-referenced against the permit so that employees could better understand what is meant by being in compliance, to encourage a proactive approach.
The training also helped to develop an awareness of Best Available Technique (BAT) as their sector’s (Textiles) BAT Reference documents will be up for renewal, potentially with new or altered requirements. See the Bref documents here.
CAR (Compliance Assessment Reports)
The training also touched on Compliance Assessment Reports. If EA staff carry out an assessment, inspection or attend an incident, they will complete a Compliance Assessment Report (CAR) and provide the business with a copy.
The CAR will record anything that the business has been doing that does not comply with their permit and will state what the business must to do to correct this, with deadlines for completion.
If a business doesn’t disclose preventative actions taken when in breach of permit limits, then a CAR report could be used as evidence used against a business if the EA wanted to prosecute.
Permit variations
Additionally, staff were made aware that any changes to processes may require a permit variation, which can take 18 months. If a business or organisation wants to conduct an activity that isn’t currently covered by their environmental permit, they must apply to have it added.
Engineering departments, for example, need to be aware that new decisions may result in the need for a permit variation, for example, if the department needed to put in a medium combustion plant, there would be a potential need for a permit variation.
Schedule 5 under the Environment Agency
The training also fostered a proactive approach among employees, as it covered environmental incident reporting.
Under Schedule 5 you must report on certain information to the EA. An operator must notify if there is any malfunction, breakdown or failure of equipment or techniques, or an accident or emission of a substance which has caused, is causing or may cause significant pollution.
The EA issues Schedule 5 notices to request additional information or clarification after an environmental permit application has been submitted. These notices are time-limited, and failure to respond correctly or within the required timeframe may result in the application being withdrawn or returned, which would be at a cost to the business.
Testimonial
We have worked with EMS previously, so decided to use them to train our employees in understanding the requirements and our organisation’s obligations in respect of our Environmental Permit. The training was well structured and superbly delivered by Becky. The bespoke structure of the course and practical exercises using our own data was extremely engaging and informative for our staff. The positive feedback from all of the attendees was testament to the effectiveness and quality of the course. Thanks again Becky!
— Ian Rawcliffe, Pincroft Dyeing and Printing